The Importance of Accurate Measurements in Drywall Framing
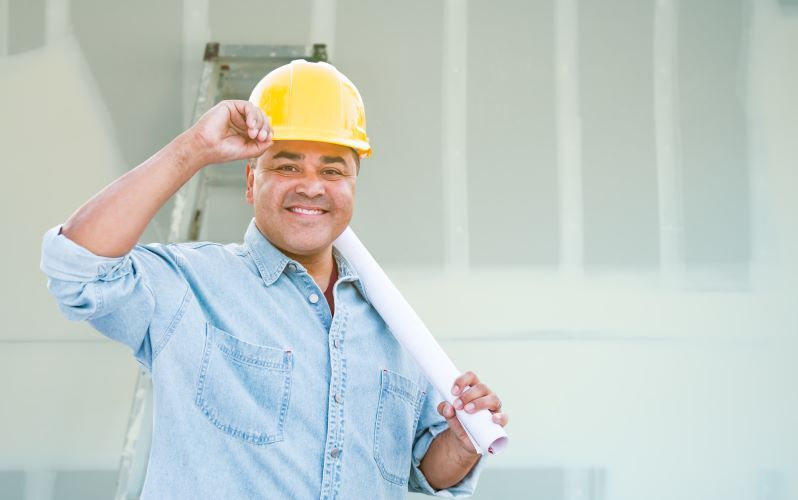
When it comes to building a durable and visually appealing interior, drywall framing is a crucial element in the construction process. Ensuring the drywall fits seamlessly into your space not only enhances the aesthetics but also adds to the overall structural integrity of the walls. One of the most important aspects of drywall framing is accurate measurement.
At London Drywallers, we know that precision in framing can make all the difference in the outcome of your project. Let’s explore why accurate measurements are key in drywall framing and how they contribute to a successful project.
Why Accurate Measurements Matter in Drywall Framing
- Structural Integrity Accurate measurements are essential for ensuring the structural soundness of your drywall installation. Poorly framed walls can lead to weak points where drywall sheets do not sit flush against the studs, resulting in cracks, loose panels, or even sagging. Accurate measurements allow for tight, consistent connections between the drywall and the framing, ensuring the strength and durability of the finished walls.
- Avoiding Material Waste Drywall sheets come in standard sizes, and framing errors can lead to miscuts, meaning more waste and higher costs. By taking the time to measure properly, you can avoid cutting too much off your drywall sheets or leaving gaps that need to be patched up. Accurate framing ensures that the drywall sheets fit perfectly, reducing the need for extra material or repairs down the line.
- Smooth Drywall Finish Precision in framing directly affects the appearance of your drywall once installed. When measurements are off, drywall sheets may not line up perfectly at the seams, creating uneven joints or noticeable bulges. This can lead to more time spent taping, mudding, and sanding, which delays the project and increases labor costs. Properly measured and framed walls create smoother transitions, making it easier to achieve a professional finish with minimal touch-ups.
- Electrical and Plumbing Accommodations Accurate drywall framing is essential for incorporating electrical outlets, light fixtures, switches, and plumbing into your walls. If your framing measurements are incorrect, these features may not align properly with the drywall, causing gaps, exposed wires, or even the need for re-framing to accommodate plumbing or wiring changes. Taking precise measurements in the framing stage ensures that everything lines up correctly, so you won’t run into complications later.
How to Ensure Accurate Measurements in Drywall Framing
- Measure Twice, Cut Once This age-old construction rule applies perfectly to drywall framing. Taking the time to measure carefully will help you avoid costly mistakes down the road. Before you cut any materials, double-check your measurements for accuracy.
- Use the Right Tools Having the right tools is essential for precise measurements. Use a reliable tape measure, a framing square for corners, and a level to ensure the walls are straight and plumb. Laser levels can also be useful for larger projects where long distances need to be measured with precision.
- Account for Drywall Thickness When framing, it’s important to account for the thickness of the drywall you plan to install. The most common drywall thickness for residential walls is 1/2 inch, but 5/8 inch is often used for ceilings and soundproofing. Knowing the thickness beforehand helps you adjust the framing layout, ensuring that drywall edges align properly with the studs.
- Proper Spacing of Studs Stud spacing plays a vital role in the strength of the drywall installation. The standard spacing for studs is 16 inches on center, but this can vary depending on the project specifications. Accurate spacing allows for better support of the drywall sheets, minimizing the risk of sagging or movement after installation. Ensure your measurements are consistent along the entire wall to avoid any irregularities.
- Pay Attention to Openings Doorways, windows, and other openings in the wall require special attention when framing. Precise measurements ensure that drywall can be installed smoothly around these features without the need for excessive cutting or patching. Accurately measured and framed openings also contribute to the overall stability and visual appeal of the finished wall.
The Benefits of Professional Drywall Framing
While some may attempt DIY drywall framing, hiring professionals ensures that every detail is accounted for, and the project is done to the highest standard. At London Drywallers, we understand the importance of accurate measurements in framing. Our team of experienced drywall professionals ensures that every cut, seam, and joint is perfect, providing a flawless finish that stands the test of time.
Key benefits of choosing professional drywall framing include:
- Reduced Material Waste: Expert measurement techniques ensure you’re not wasting drywall sheets or other materials due to misalignment or miscuts.
- Quicker Installation: Professionals know how to measure and cut efficiently, speeding up the entire drywall installation process.
- Long-Lasting Durability: With accurate framing, your drywall is securely fastened, preventing cracks, loose panels, or warping in the future.
- Flawless Appearance: Professional framing results in smoother drywall surfaces and more even seams, requiring less work during the finishing stages.
Conclusion
Accurate measurements are the foundation of successful drywall framing. Whether you're building new walls, renovating a space, or installing drywall in your garage, precision is key to ensuring a seamless and durable finish. Properly framed walls not only improve the appearance of your space but also enhance its structural integrity.
At London Drywallers, we specialize in drywall framing and installation, providing top-quality craftsmanship for both residential and commercial projects. If you're planning a drywall project and want to ensure the best results, contact us today. Let our experts handle the framing so you can enjoy flawless walls and ceilings for years to come.
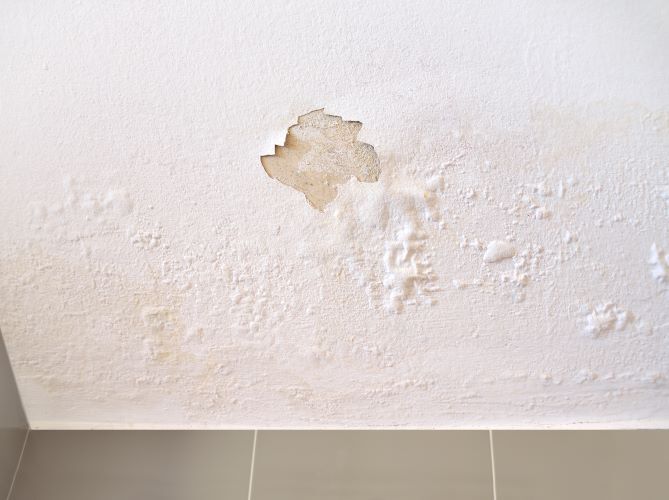
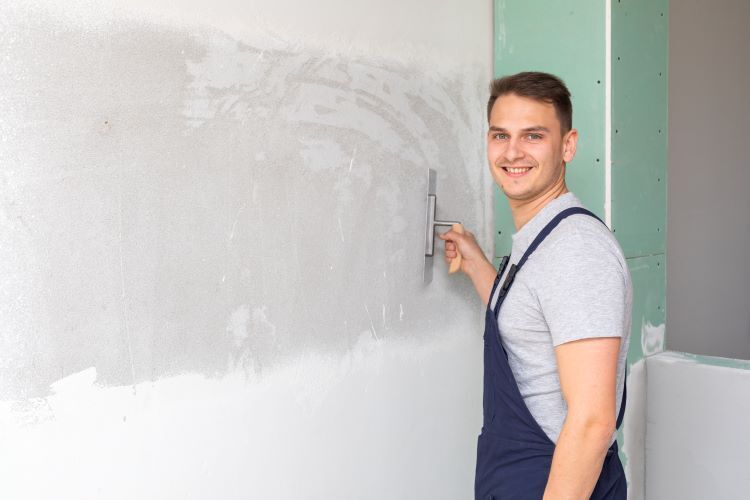
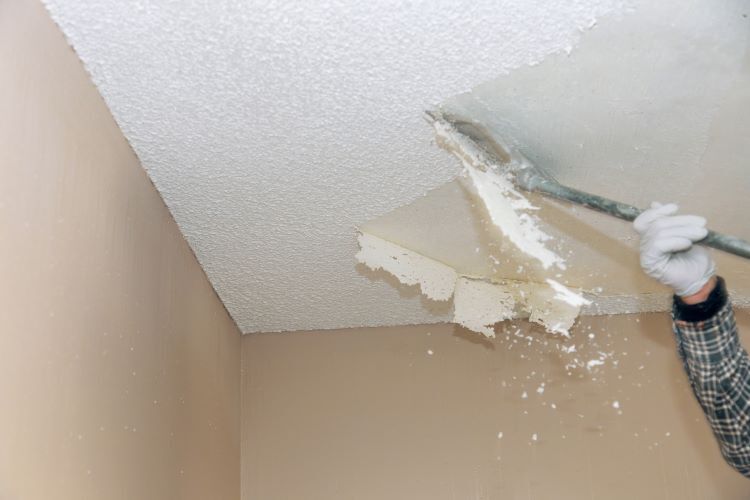
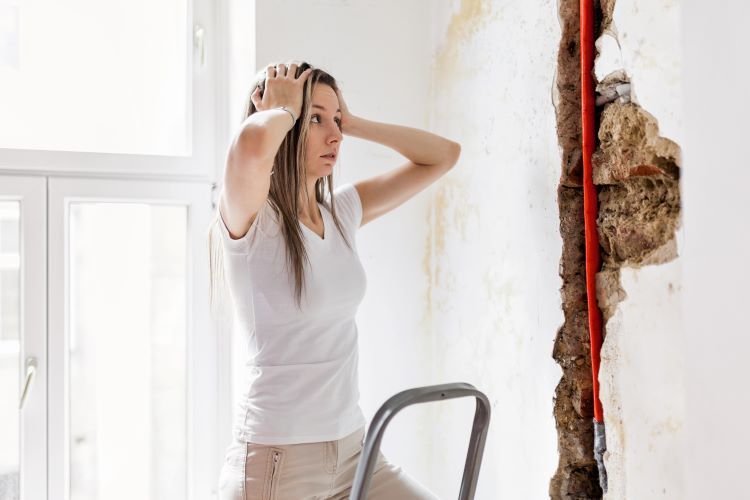
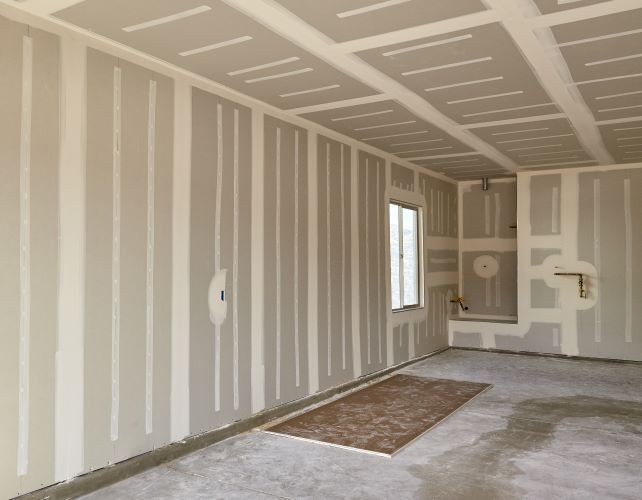
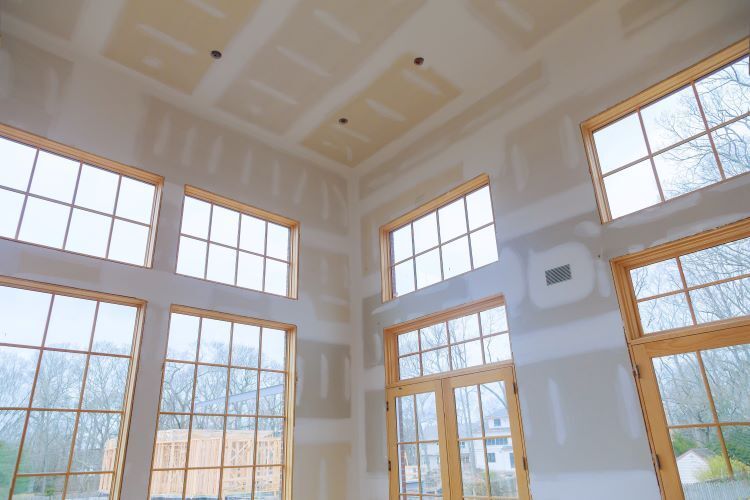
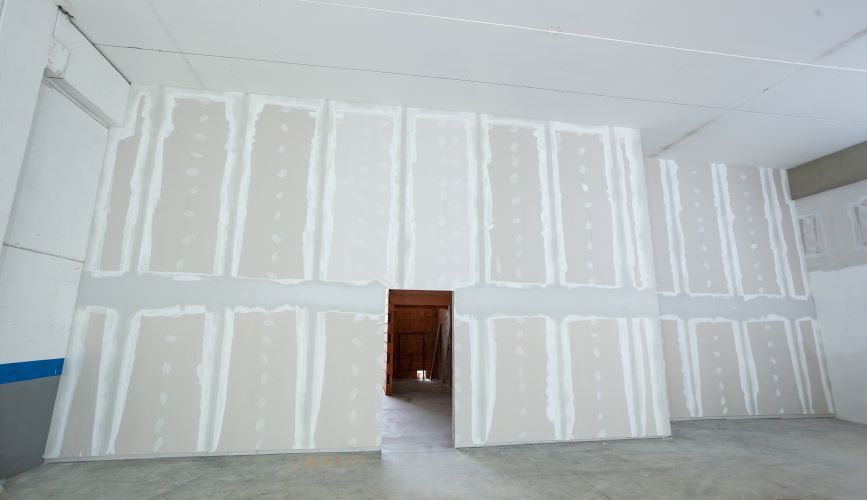
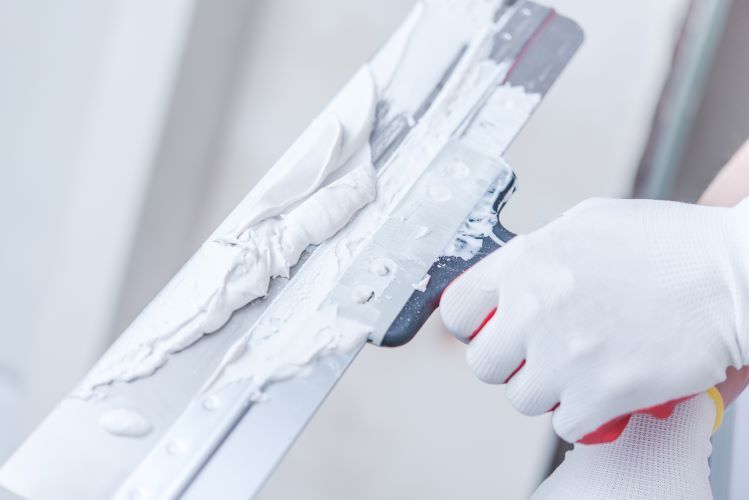
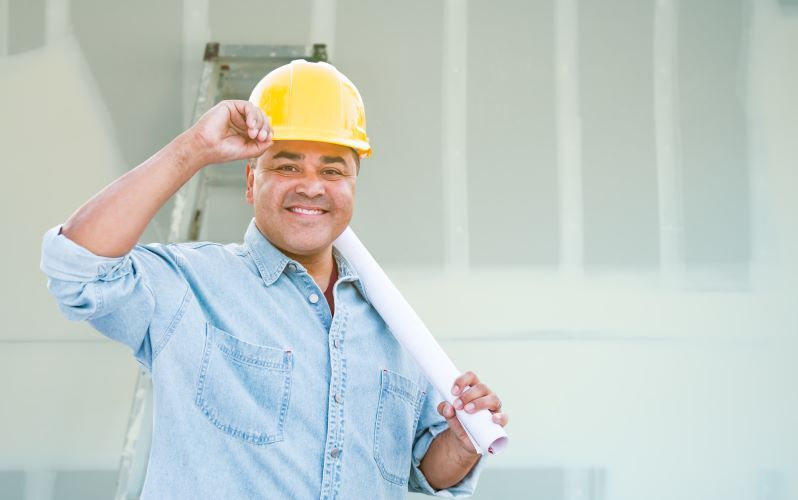
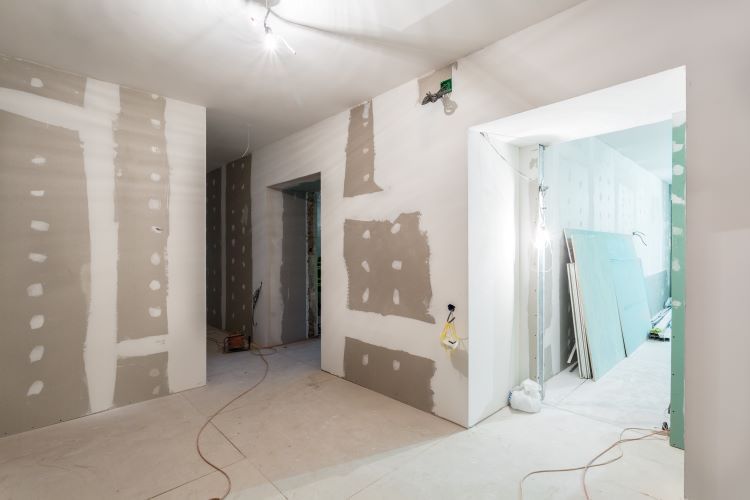